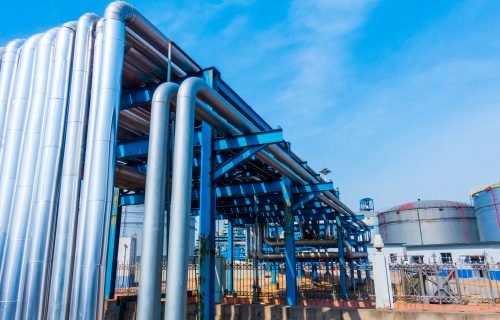
The Pikotek VCS gasket is a high reliability gasket used for both isolating and general sealing purposes in Very Critical Services. The gasket has a proven track record of integrity in aggressive sealing situations. The VCS is suitable in all services up to and including ANSI 2500# and API 10,000# classes. The VCS is designed for service where the cost of gasket failure cannot be tolerated. The VCS gasket consists of a PTFE (Teflon) spring-energized face seal, or an elastomeric o-ring, seated in an isolating laminate, which is permanently bonded to a high-strength metal gasket core.
Due to its unique pressure activated sealing mechanism, the gasket requires far less bolt stress to seal than any other gasket. The VCS gasket inner diameter is exactly matched to the flange bore to eliminate turbulent flow and flange face erosion/corrosion. The seal elements are replaceable in the reusable gasket retainer.
VCS Metallic Core
The core of each gasket is made of annealed 316 stainless steel. Other metals, including Duplex and Inconel are available upon special order.
The sealing elements are intended to provide an impervious barrier through which no contained media or other substance can penetrate. Consequently, the composite retainer backing material behind the seal remains uncontaminated and thus permanently holds the seal in place in a static, fully encapsulated manner.
Recommended for all environments. Helical wound spring provides radial load. Encapsulation in the seal groove eliminates creep or cold flow. This sealing system truly distinguishes Pikotek gaskets from all other flange sealing systems.
Temperature Range: -250° F to +392° F (note: gasket material is limiting factor)
General-purpose oilfield elastomer. Excellent resistance to aliphatic hydrocarbons, glycols and H2S. Good resistance to aromatic hydrocarbons.VCS Tech7.8 Final.indd 4 7/9/09 1:38 PMNot recommended for: Systems with amine inhibitors and in piping systems containing significant partial pressures of polar gases (i.e. CO2) where radical pressure drops (i.e., 2000 PSI to 0 PSI) commonly occur.Temperature Range: -15° F to +392° F
GRE (Glass-Reinforced Epoxy) tubing is suitable for continuous exposure to 302° F. This material is an epoxy laminate that offers excellent resistance to crushing, cracking, breaking and thread pinch.
Nomex is a high temperature sleeve material manufactured from solid organic polymer and is suitable for temperatures up to 425 degree F.
Spiral wound Mylar is a general-purpose material recommended for bolting applications with flange temperatures below 250° F. This material has generally fair resistance to crushing, cracking, breaking and thread pinch.
ANSI B16.5 Bolt Torque (ft.-lbs) for 7500psi Gasket Seating Stress for RTJ FlangesPressure Classes
VCS Metallic Core
The core of each gasket is made of annealed 316 stainless steel. Other metals, including Duplex and Inconel are available upon special order.
The sealing elements are intended to provide an impervious barrier through which no contained media or other substance can penetrate. Consequently, the composite retainer backing material behind the seal remains uncontaminated and thus permanently holds the seal in place in a static, fully encapsulated manner.
Recommended for all environments. Helical wound spring provides radial load. Encapsulation in the seal groove eliminates creep or cold flow. This sealing system truly distinguishes Pikotek gaskets from all other flange sealing systems.
Temperature Range: -250° F to +392° F (note: gasket material is limiting factor)
General-purpose oilfield elastomer. Excellent resistance to aliphatic hydrocarbons, glycols and H2S. Good resistance to aromatic hydrocarbons.VCS Tech7.8 Final.indd 4 7/9/09 1:38 PMNot recommended for: Systems with amine inhibitors and in piping systems containing significant partial pressures of polar gases (i.e. CO2) where radical pressure drops (i.e., 2000 PSI to 0 PSI) commonly occur.Temperature Range: -15° F to +392° F
GRE (Glass-Reinforced Epoxy) tubing is suitable for continuous exposure to 302° F. This material is an epoxy laminate that offers excellent resistance to crushing, cracking, breaking and thread pinch.
Nomex is a high temperature sleeve material manufactured from solid organic polymer and is suitable for temperatures up to 425 degree F.
Spiral wound Mylar is a general-purpose material recommended for bolting applications with flange temperatures below 250° F. This material has generally fair resistance to crushing, cracking, breaking and thread pinch.
ANSI B16.5 Bolt Torque (ft.-lbs) for 7500psi Gasket Seating Stress for RTJ FlangesPressure Classes
Here is the value we bring to you
Our decades of hands-on field experience from unconventional environments to compliance and safety, allows us to understand what you need down to the smallest detail.