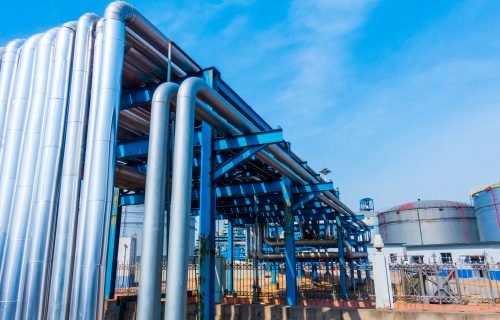
Interested in the Evolution Isolation Gasket? Get in touch!
Conditions are changing. As we drill deeper and utilize enhanced recovery methods such as thermal and CO2 injection, we are exposing the products in our pipelines to greater concentrations of harsh chemicals, higher temperatures and higher pressures. In addition, it is estimated that 40% of the world’s remaining gas reserves are sour, and CO2 and/or H2S content within these wells averages 10% or more. Maintaining pipeline integrity and keeping emissions in check has never been more important. Yet, traditional pipeline materials, including gaskets and seals, are not always up to the challenge. That is why we are proud to introduce Evolution, a fully-encapsulated isolation gasket that delivers the impermeable performance needed to prepare any flange for the increasing risks found in today’s oil and gas industry.
EVOLUTION® is a patent pending product that is the first of its kind to be a fully encapsulated isolating gasket. The thinner, 1/8” (3mm) design minimizes the difficulties often encountered while attempting to install thicker isolating gaskets. The total encapsulation allows the gasket to be hydro-tested and kept in the pipeline with virtually no loss in isolation properties.
This innovative gasket is coated using a GPT proprietary material designed specifically for the oil and gas industry that is extremely abrasion and impact resistant. The coating is also chemically resistant to attack from H₂S, steam, CO, CO₂, and other chemicals found in oil and gas pipelines.
EVOLUTION® has passed API 6FB fire testing in multiple sizes and pressure classes and has a considerable increase in operating temperature over GRE products. Furthermore, EVOLUTION® does not have the permeation issues or chemical attack that plagues GRE gaskets.
Under harsh conditions, gaskets made from GRE may be vulnerable to chemical attack, blowout, thermal attack, hydrolysis and emissions —all of which can have serious consequences. EVOLUTION® is different. Its revolutionary materials and design provides industry-leading resistance to leakage and flange corrosion, as well as unprecedented levels of fire safety.
EVOLUTION® provides the highest pressure rating of any isolating gasket available. Unlike GRE gaskets, which are prone to delamination, EVOLUTION® has no laminations and as a result can better withstand high-pressure environments.
Rated to 500°F (260°C)*, EVOLUTION® can also operate under high temperatures. Tested comprehensively for safety, the product has API 6FB, 3rd Edition Fire Test recognition.
* When used with Mica sleeves and washers
*For higher temperature applications, please order MICA sleeves and MICA washers.
Carrier: 316L stainless steel core with Fully Encapsulating GPT Proprietary Coating
Colour: Dark brown with black handle
Fluid Services: Oil and Gas
Maximum Operating Temperature (°F/°C): 500°F/260°C**
Minimum Operating Temperature: (minus): -58°F/-50°C
Size: 0.5-24 inch NPS (larger sizes possible, call us)
Maximum Pressure Class: ASME B16.5 150# – 2500#, API 6A 2K-5K*
Test | Value | Test Method |
---|---|---|
Water Absorption (%): | 0.046 | ASTM D570 |
Sealability Test: | .0011ml/min | ASTM F37 |
Compression Test: | 140 MPa | EN 13555 @ 260° C |
Creep Relaxation: | 1.0 | EN 13555 @ 260° C |
Leakage Test: | 2.9×10-11 mg/m/s | EN 13555 @ 40 bar Helium @ 135 Mpa gasket stress) |
Hot Blowout Test: | No blowout | HOBT @ 260° C @ 62.3 bar |
Dielectric Strength: | 1400 Volts/ Mil | ASTM D149 (Short Time) |
Tensile Strength Gasket: | 70,000 psi | ASTM D638 |
Salt Spray Test: | 3000 hours – No Visible Effect | ASTM B11 |
This is a general guide and should not be the sole means of selecting or rejecting this material.
* Values are typical and do not constitute specification Limits
** Temperature rating when using Mica sleeves/washers
1 All isolation products are affected by exposure to heat and moisture where electrical isolation is concerned.
Please note that field values may vary from test values due to exposure to one or both of these environmental factors.
Conditions are changing. As we drill deeper and utilize enhanced recovery methods such as thermal and CO2 injection, we are exposing the products in our pipelines to greater concentrations of harsh chemicals, higher temperatures and higher pressures. In addition, it is estimated that 40% of the world’s remaining gas reserves are sour, and CO2 and/or H2S content within these wells averages 10% or more. Maintaining pipeline integrity and keeping emissions in check has never been more important. Yet, traditional pipeline materials, including gaskets and seals, are not always up to the challenge. That is why we are proud to introduce Evolution, a fully-encapsulated isolation gasket that delivers the impermeable performance needed to prepare any flange for the increasing risks found in today’s oil and gas industry.
EVOLUTION® is a patent pending product that is the first of its kind to be a fully encapsulated isolating gasket. The thinner, 1/8” (3mm) design minimizes the difficulties often encountered while attempting to install thicker isolating gaskets. The total encapsulation allows the gasket to be hydro-tested and kept in the pipeline with virtually no loss in isolation properties.
This innovative gasket is coated using a GPT proprietary material designed specifically for the oil and gas industry that is extremely abrasion and impact resistant. The coating is also chemically resistant to attack from H₂S, steam, CO, CO₂, and other chemicals found in oil and gas pipelines.
EVOLUTION® has passed API 6FB fire testing in multiple sizes and pressure classes and has a considerable increase in operating temperature over GRE products. Furthermore, EVOLUTION® does not have the permeation issues or chemical attack that plagues GRE gaskets.
Under harsh conditions, gaskets made from GRE may be vulnerable to chemical attack, blowout, thermal attack, hydrolysis and emissions —all of which can have serious consequences. EVOLUTION® is different. Its revolutionary materials and design provides industry-leading resistance to leakage and flange corrosion, as well as unprecedented levels of fire safety.
EVOLUTION® provides the highest pressure rating of any isolating gasket available. Unlike GRE gaskets, which are prone to delamination, EVOLUTION® has no laminations and as a result can better withstand high-pressure environments.
Rated to 500°F (260°C)*, EVOLUTION® can also operate under high temperatures. Tested comprehensively for safety, the product has API 6FB, 3rd Edition Fire Test recognition.
* When used with Mica sleeves and washers
*For higher temperature applications, please order MICA sleeves and MICA washers.
Carrier: 316L stainless steel core with Fully Encapsulating GPT Proprietary Coating
Colour: Dark brown with black handle
Fluid Services: Oil and Gas
Maximum Operating Temperature (°F/°C): 500°F/260°C**
Minimum Operating Temperature: (minus): -58°F/-50°C
Size: 0.5-24 inch NPS (larger sizes possible, call us)
Maximum Pressure Class: ASME B16.5 150# – 2500#, API 6A 2K-5K*
Test | Value | Test Method |
---|---|---|
Water Absorption (%): | 0.046 | ASTM D570 |
Sealability Test: | .0011ml/min | ASTM F37 |
Compression Test: | 140 MPa | EN 13555 @ 260° C |
Creep Relaxation: | 1.0 | EN 13555 @ 260° C |
Leakage Test: | 2.9×10-11 mg/m/s | EN 13555 @ 40 bar Helium @ 135 Mpa gasket stress) |
Hot Blowout Test: | No blowout | HOBT @ 260° C @ 62.3 bar |
Dielectric Strength: | 1400 Volts/ Mil | ASTM D149 (Short Time) |
Tensile Strength Gasket: | 70,000 psi | ASTM D638 |
Salt Spray Test: | 3000 hours – No Visible Effect | ASTM B11 |
This is a general guide and should not be the sole means of selecting or rejecting this material.
* Values are typical and do not constitute specification Limits
** Temperature rating when using Mica sleeves/washers
1 All isolation products are affected by exposure to heat and moisture where electrical isolation is concerned.
Please note that field values may vary from test values due to exposure to one or both of these environmental factors.
Our decades of hands-on field experience, from unconventional environments to compliance and safety, allows us to understand what you need - down to the smallest detail.