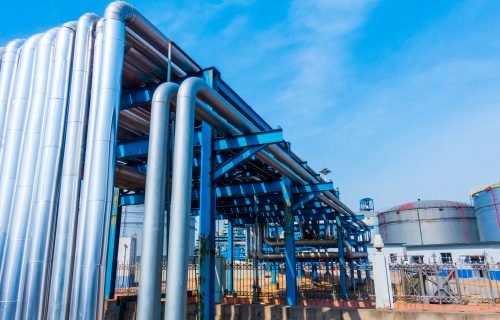
The ElectroStop® monolithic isolation fitting is considered to have the industry’s best Dual O-Ring Seal. The ElectroStop® will serve as a positive, leak-proof, block against the flow of electric current in all piping systems. When you bury it you also bury maintenance costs; an especially important feature for system operators and engineers.
Bolts, sleeves and washers – the major source of short circuits in most isolation assemblies – are eliminated with the ElectroStop® isolation joint. Each joint is electrically tested during production to assure integrity, performance, isolating properties.
The ElectroStop® isolation joint is completely factory assembled and tested. There are no flanges, gaskets, nuts, bolts, sleeves or washers to handle and consequently no fluid leaks due to improper field assembly.
A two-part bonded epoxy is sprayed to a thickness of .016” -.024” (.40 to .60mm) to within 2” (50.8mm) of each weld end. Each joint is tested for coating thickness uniformity and for holidays.
All ElectroStop® fittings undergo hydrostatic pressure tests at 1.5 times rated operating pressure in accordance with ASME B31.3 standards. Testing is normally conducted for 30 minutes for joints up to 6” and 60 minutes for 8” to 24” joints but can be tested per customer specifications. A pneumatic test is held at 87 psi for 10 minutes.
All ElectroStop® fittings undergo a weld inspection with combinations of ultrasonic (UT) and magnetic partical (MT) on all welds. In addition, X-ray tests can be conducted upon request.
Manufactured under an ISO 9001:2008 Quality Management System. The ElectroStop® is available in any diameter and any ANSI Class
To order ElectroStop™ Monolithic Isolating Fittings please indicate the following:
Monolithic isolation fittings are boltless and completely factory assembled in accordance with the appropriate requirements of ASTM, API, DIN and BS codes. All welds shall be butt weld construction. The dielectric isolation material shall be a thermosetting fiberglass epoxy material. Sealing shall be by two (2) static, self energized O ring seals housed in accurately machined grooves, fully protected from cavitation in full compliance with ASME design codes. Interior and exterior coating shall be a two part epoxy with a thickness of 12 to 15 mils to within 2” of each end. Testing shall be Electrical (@5kv, 25 Mohm), Hydraulic (@ 1.5 x O.P.) and Weld (Ultrasonic/Magnetic Particle/Dye Penetrant).
The Monolithic Isolation Fitting shall be the ElectroStop™ Isolation Fitting as manufactured by Pipeline Seal & Insulator, Inc., Houston, Texas.
Each monolithic isolation fitting shall be manufactured at a facility that has a Registered ISO 9001:2000 Quality Management System. Copy of current ISO 9001:2000 Registration shall be provided with material submittal.
ElectroStop™ isolation fittings provide permanent electrical isolation of piping sections, facilitating the management of a cathodic protection system. These fittings will be completely factory assembled.
* See Note.
* See Note.
*Note: All data supplied is for standard fittings. Please contact factory for nominal diameters, pressures (up to 2500 ANSI), temperatures (up to 160° C, 320° F.) and electrical characteristics not shown. The information is subject to change at the manufacturer’s discretion.
All products are warranted against failure caused by manufacturing defects for a period of one year. Any product found to be so defective and returned within one year from date of shipment will be replaced without charge. The above warranty is made in lieu of, and we disclaim, any and all other warranties, expressed or implied, including the warranties of merchantability and fitness for a particular purpose, and buyer agrees to accept the products without any such warranties. We hereby disclaim any obligation or liability for consequential damages, labor costs or any other claims or liabilities of any kind whatsoever.
The ElectroStop™ is a complete factory assembled and tested monolithic isolation fitting which will serve as a leak proof, long lasting block against the flow of electrical current in steel piping systems. Care should be used during the handling and installation process so as not to damage the fitting.
Only two (2) welds are required for installation.
The ElectroStop™ may be installed either above grade or buried below grade.
Note: WHEN INSTALLING IN A VERTICAL POSITION ABOVE GRADE, THE WELDED END OF THE COLLAR (HUB) SHOULD FACE UP.
The end filled with the epoxy fill (opposite end of the welded collar of hub) can have a concave area and possibly retain moisture and can be sensitive to ultra violet light exposure.
THE SUGGESTIONS BELOW SHOULD NOT PRECLUDE THE FOLLOWING OF ALL COMPANY, LOCAL, STATE, OR FEDERAL CODES AND/OR SAFETY REQUIREMENTS AND/OR REGULATIONS. DESIGN CONCERNS, INCLUDING ELECTRICAL SAFETY PRECAUTIONS, GROUNDING, MECHANICAL STRESSES, ETC. SHOULD BE ADDRESSED PRIOR TO USE OR INSTALLATION. ALWAYS WEAR PROPER SAFETY EQUIPMENT FOR PERSONAL PROTECTION. CONSULT WITH YOUR COMPANY.
The ElectroStop™ fitting should be installed just like any other weld-in fitting or piece of pipe with the only exceptions being:
The pipe pups on the ElectroStop™ are intended to act somewhat as a heat sink and should not be shortened. If the fitting is too long for the installation location, cut the needed length out of the existing piping, not the ElectroStop®.
During the welding operation a temperature sensor such as a thermometer or thermocouple should be secured to the collar (hub) of the ElectroStop™. As a precautionary procedure, wet rags or other cooling methods are sometimes used to reduce heat at the collar (hub) area.
COATING
After the welding operation is completed, The ElectroStop™ fitting and welds should be prepared for your corrosion protection coating or tape just like any other bare or shop coated fitting or piece of pipe.
SUPPORT AND BACKFILLING
Care should be used to assure uniform support and compaction around the entire ElectroStop™ fitting. Undo mechanical stresses caused by improper support or backfilling could cause damage to the ElectroStop™ that could result in leakage.
TESTING AND CERTIFICATION
All ElectroStop™ fittings undergo a weld inspection with combinations of ultrasonic (UT), magnetic particle (MT) and dye penetrant (LT) on all welds. X-Ray tests are preformed upon request.
We certify that each standard order ElectroStop™ will be factory tested at 1-1/2 times the rated operating pressure for the amount of time listed below and in accordance to the latest ANSI Standards.
Pipe Size | Hydrostatic Minimum Test Time |
2″-4″ | 30 minutes |
8″-24″ | 60 minutes |
After completion of the hydrostatic tests, The ElectroStop™ are electrically tested to assure an electrical resistance of 25 Mohms (wet or dry conditions @ 20( C) @ 1kv D.C. and a minimum breakdown voltage of 5kv @ 50 hz for 1 minute.
Control over all stages of production is ensured by close adherance to an in-place and ongoing ISO 9001 Quality Assurance Program which is constantly monitored and subject to periodic outside audit. A qualified inspector witnesses all tests.
Monolithic isolation fittings are boltless and completely factory assembled in accordance with the appropriate requirements of ASTM, API, DIN and BS codes. All welds shall be butt weld construction. The dielectric isolation material shall be a thermosetting fiberglass epoxy material. Sealing shall be by two (2) static, self energized O ring seals housed in accurately machined grooves, fully protected from cavitation in full compliance with ASME design codes. Interior and exterior coating shall be a two part epoxy with a thickness of 12 to 15 mils to within 2” of each end. Testing shall be Electrical (@5kv, 25 Mohm), Hydraulic (@ 1.5 x O.P.) and Weld (Ultrasonic/Magnetic Particle/Dye Penetrant).
The Monolithic Isolation Fitting shall be the ElectroStop™ Isolation Fitting as manufactured by Pipeline Seal & Insulator, Inc., Houston, Texas.
Each monolithic isolation fitting shall be manufactured at a facility that has a Registered ISO 9001:2000 Quality Management System. Copy of current ISO 9001:2000 Registration shall be provided with material submittal.
ElectroStop™ isolation fittings provide permanent electrical isolation of piping sections, facilitating the management of a cathodic protection system. These fittings will be completely factory assembled.
* See Note.
* See Note.
*Note: All data supplied is for standard fittings. Please contact factory for nominal diameters, pressures (up to 2500 ANSI), temperatures (up to 160° C, 320° F.) and electrical characteristics not shown. The information is subject to change at the manufacturer’s discretion.
All products are warranted against failure caused by manufacturing defects for a period of one year. Any product found to be so defective and returned within one year from date of shipment will be replaced without charge. The above warranty is made in lieu of, and we disclaim, any and all other warranties, expressed or implied, including the warranties of merchantability and fitness for a particular purpose, and buyer agrees to accept the products without any such warranties. We hereby disclaim any obligation or liability for consequential damages, labor costs or any other claims or liabilities of any kind whatsoever.
The ElectroStop™ is a complete factory assembled and tested monolithic isolation fitting which will serve as a leak proof, long lasting block against the flow of electrical current in steel piping systems. Care should be used during the handling and installation process so as not to damage the fitting.
Only two (2) welds are required for installation.
The ElectroStop™ may be installed either above grade or buried below grade.
Note: WHEN INSTALLING IN A VERTICAL POSITION ABOVE GRADE, THE WELDED END OF THE COLLAR (HUB) SHOULD FACE UP.
The end filled with the epoxy fill (opposite end of the welded collar of hub) can have a concave area and possibly retain moisture and can be sensitive to ultra violet light exposure.
THE SUGGESTIONS BELOW SHOULD NOT PRECLUDE THE FOLLOWING OF ALL COMPANY, LOCAL, STATE, OR FEDERAL CODES AND/OR SAFETY REQUIREMENTS AND/OR REGULATIONS. DESIGN CONCERNS, INCLUDING ELECTRICAL SAFETY PRECAUTIONS, GROUNDING, MECHANICAL STRESSES, ETC. SHOULD BE ADDRESSED PRIOR TO USE OR INSTALLATION. ALWAYS WEAR PROPER SAFETY EQUIPMENT FOR PERSONAL PROTECTION. CONSULT WITH YOUR COMPANY.
The ElectroStop™ fitting should be installed just like any other weld-in fitting or piece of pipe with the only exceptions being:
The pipe pups on the ElectroStop™ are intended to act somewhat as a heat sink and should not be shortened. If the fitting is too long for the installation location, cut the needed length out of the existing piping, not the ElectroStop®.
During the welding operation a temperature sensor such as a thermometer or thermocouple should be secured to the collar (hub) of the ElectroStop™. As a precautionary procedure, wet rags or other cooling methods are sometimes used to reduce heat at the collar (hub) area.
COATING
After the welding operation is completed, The ElectroStop™ fitting and welds should be prepared for your corrosion protection coating or tape just like any other bare or shop coated fitting or piece of pipe.
SUPPORT AND BACKFILLING
Care should be used to assure uniform support and compaction around the entire ElectroStop™ fitting. Undo mechanical stresses caused by improper support or backfilling could cause damage to the ElectroStop™ that could result in leakage.
TESTING AND CERTIFICATION
All ElectroStop™ fittings undergo a weld inspection with combinations of ultrasonic (UT), magnetic particle (MT) and dye penetrant (LT) on all welds. X-Ray tests are preformed upon request.
We certify that each standard order ElectroStop™ will be factory tested at 1-1/2 times the rated operating pressure for the amount of time listed below and in accordance to the latest ANSI Standards.
Pipe Size | Hydrostatic Minimum Test Time |
2″-4″ | 30 minutes |
8″-24″ | 60 minutes |
After completion of the hydrostatic tests, The ElectroStop™ are electrically tested to assure an electrical resistance of 25 Mohms (wet or dry conditions @ 20( C) @ 1kv D.C. and a minimum breakdown voltage of 5kv @ 50 hz for 1 minute.
Control over all stages of production is ensured by close adherance to an in-place and ongoing ISO 9001 Quality Assurance Program which is constantly monitored and subject to periodic outside audit. A qualified inspector witnesses all tests.
Here is the value we bring to you
Our decades of hands-on field experience from unconventional environments to compliance and safety, allows us to understand what you need down to the smallest detail.